齒輪加工中,材料硬度與平齒機(jī)刀具的匹配關(guān)系直接影響加工效率、刀具壽命及齒輪精度,需從材料特性、刀具選型和工藝參數(shù)三方面綜合優(yōu)化。
1. 材料硬度分類及刀具匹配原則
齒輪材料按硬度可分為三類:
- 低硬度材料(HRC<30):如未熱處理的20CrMnTi、45#鋼等,適合高速鋼(HSS)刀具。此類材料切削阻力小,HSS刀具兼具韌性與經(jīng)濟(jì)性。
- 中高硬度材料(HRC30-50):如調(diào)質(zhì)處理的40Cr、42CrMo,需選用硬質(zhì)合金刀具(如YG8、YW2)。硬質(zhì)合金硬度達(dá)HRA89-93,耐磨性優(yōu)異,可承受較高切削溫度。
- 超高硬度材料(HRC>50):滲碳淬火齒輪(如20CrNiMo)或粉末冶金件,需采用涂層硬質(zhì)合金(TiAlN涂層)或立方氮化硼(CBN)刀具。CBN硬度僅次于金剛石,耐高溫達(dá)1400℃,可加工HRC60以上材料。
2. 刀具選型關(guān)鍵技術(shù)
- 涂層技術(shù):TiN/TiCN涂層可提升刀具表面硬度20%-30%,Al?O?涂層耐熱性優(yōu)異,適用于高速干切。
- 幾何參數(shù)優(yōu)化:加工高硬度材料時(shí),采用負(fù)前角(-5°~-10°)增強(qiáng)刃口強(qiáng)度,后角6°-8°減少摩擦,螺旋角30°-45°改善排屑。
- 抗沖擊設(shè)計(jì):對(duì)斷續(xù)切削工況(如斜齒輪加工),選擇細(xì)晶粒硬質(zhì)合金或增韌具,提升抗崩刃能力。
3. 工藝參數(shù)協(xié)同控制
- 切削速度:硬質(zhì)材料宜采用中低速(80-150m/min),避免熱軟化效應(yīng)導(dǎo)致刃口粘連。
- 冷卻策略:高硬度齒輪加工推薦高壓內(nèi)冷(壓力>7MPa),有效降低切削區(qū)溫度并輔助斷屑。
- 進(jìn)給量匹配:HRC>45時(shí),進(jìn)給量需控制在0.05-0.1mm/r,避免刀具過(guò)載。
實(shí)際應(yīng)用中,需結(jié)合齒輪批量、精度要求(如ISO 6-8級(jí))及設(shè)備剛性動(dòng)態(tài)調(diào)整。例如,批量生產(chǎn)滲碳齒輪時(shí),采用CBN刀具配合微量潤(rùn)滑(MQL)工藝,可提升加工效率3-5倍,同時(shí)實(shí)現(xiàn)Ra0.8μm的表面粗糙度。定期檢測(cè)刀具磨損(VB值<0.3mm)是保證加工穩(wěn)定性的關(guān)鍵。
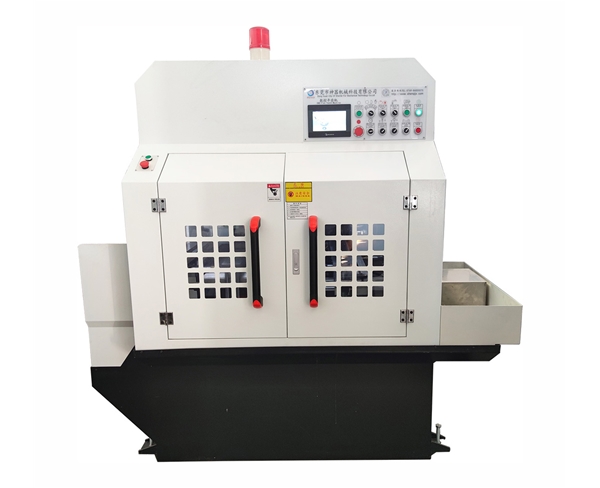